
Track, Monitor and Optimize Every Aspect of Your Supply Chain
Traceability refers to the ability to track and record the movement, origin, and history of a product, material, or process throughout its lifecycle. It ensures transparency by maintaining a detailed history of where an item originated, how it was processed, and where it was distributed.

Machine

PLC
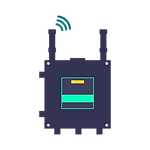
Profinet
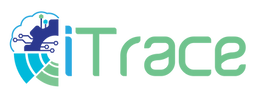
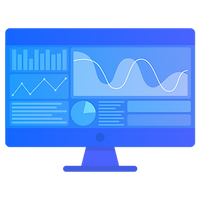
HMI DASHBOARD

We achieve traceability in both forms
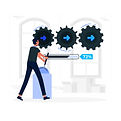
Process Traceability
Process traceability focuses on tracking every stage of production, ensuring that manufacturing standards and quality controls are met.

Product Traceability
On the other hand, product traceability follows individual products or batches across the supply chain, helping businesses track their origin, prevent counterfeiting, and facilitate recalls if necessary.
Both forms of traceability are essential for improving efficiency, ensuring regulatory compliance, and building consumer trust in industries
How Traceability Prevents Defects in Manufacturing
01
Raw Material Sourcing
Traceability ensures that all sourced metals, composites, and polymers meet industry standards. Each batch is documented with supplier details, certifications, and test reports. If any material fails to meet the required parameters, it is flagged and prevented from entering production.
02
Machining & Production
Every machine process is monitored with traceability linking components to specific machine settings, operator details, and inspection results. If a part does not meet dimensional accuracy or quality standards, it is blocked from proceeding to the next stage preventing defects from moving forward.
03
Surface Treatment & Coating
Traceability ensures that surface treatments like heat treatment, anodizing or electroplating meet exact specifications. If a part does not undergo the required curing time or fails to achieve the necessary coating thickness, the system automatically prevents it from advancing to assembly.
04
Assembly & Quality Checks
Before assembly, each component is validated for compliance. If any part has an unresolved quality issue or has bypassed a critical step, traceability blocks it from being integrated into the final system, ensuring only defect-free components are used.
05
Packaging & Logistics
Traceability ensures that only approved and verified products move to packaging and dispatch. Each unit’s serial number is checked against quality records, preventing defective or non-compliant items from reaching customers.
Enhancing Automotive Traceability with PLC and HMI Integration
In the automotive industry, integrating PLC (Programmable Logic Controllers) and HMI (Human-Machine Interface) systems streamlines traceability by automating data collection and offering real-time insights into production processes. PLCs capture data from machinery, sensors, and materials, ensuring that components meet quality standards and flagging deviations before defective parts progress further. HMI systems provide operators with an intuitive interface to monitor production, track components, and make necessary adjustments, improving overall traceability and operational efficiency.
By connecting SAP with PLCs, production data is synchronized across enterprise systems, optimizing inventory and demand planning. Integration with analytics reports and real-time feedback systems like tower lamps and the Andon system enhances decision-making by providing instant alerts about machine status or quality issues. Communication protocols like Modbus, Profibus, and Profinet ensure seamless data exchange across devices, while S7 controllers and sensors enable precise control over automated processes, ensuring continuous traceability from raw materials to the final product.
The Strategic Advantages of Traceability
Quality Control
Ensures that every component meets industry standards by preventing defective parts from progressing through production.
Supply Chain Transparency
Tracks materials and components from their origin to final assembly, reducing risks associated with counterfeit or substandard parts.
Regulatory Compliance
Helps manufacturers meet stringent automotive safety and environmental regulations by maintaining detailed records of materials, processes, and inspections.
Process Optimization
Monitors production efficiency, allowing manufacturers to refine processes, reduce downtime, and enhance productivity.
Defect Prevention & Recall Management
Identifies defective batches early in production, reducing waste and enabling targeted recalls without affecting unaffected components.
Cost Reduction
Minimizes rework, scrap, and warranty claims by ensuring only high-quality components move forward in production.
How to achieve Traceability with Technology?
Hardware
.png)
RFID
.png)
Barcodes & QR Codes

IoT Sensors

GPS
(Global Positioning System)

Blockchain for Secure Tracking
Types of Traceable Manufacturing
Supply chain traceability is primarily categorized into two types:
Forward Traceability and Backward Traceability. Additionally, manufacturing traceability includes product tracking and tracing, which further enhance visibility.

Forward Traceability
Also known as Downstream traceability, forward traceability tracks a product's journey from production to the end customer. It enables seamless tracking from raw materials to the finished product, ensuring complete visibility along the supply chain.
This type of traceability plays a crucial role in managing defective products and recalls. If an issue is identified in a specific component, forward traceability allows for quick identification and recall of affected products. As a result, it enhances customer satisfaction and strengthens brand loyalty.
Backward Traceability
Referred to as Upstream traceability, backward traceability traces a product’s path in reverse starting from the consumer and going back to its origin, including raw materials and production processes. It also enables tracking within the logistical chain, identifying the product’s movement from the end user back to the original manufacturer.
For instance, in the automotive sector, backward traceability helps track the origin of vehicle components, identifying the suppliers, manufacturing plants, and assembly processes involved before the final product reaches the customer. This is crucial for quality control, recalls, and ensuring compliance with safety standards.